Filter Media Replacement at the Big Cottonwood Water Treatment Plant
Filtration is an important part of the water treatment process
By Ken Hibbert, Salt Lake City Department of Public Utilities Water Treatment Manager
February 9, 2007
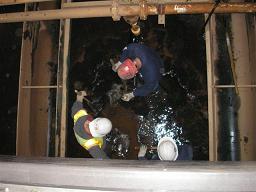
|
BCWTP filter beds are being replaced with new media. |
|
Salt Lake City’s water treatment plants represent an investment in public health. There are several steps in the water treatment process that disinfects, cleans and removes pathogens from our drinking water. Every process has a specific goal that contributes to better water quality. During this past several months the filter beds at the Big Cottonwood Plant Water Treatment Plant (“BCWTP”) have been replaced with new filter media at a cost of $650,000.
The water supply for the BCWTP is Big Cottonwood Creek locate about 10 miles south of Salt Lake City at the foot of the Wasatch Mountain Range next to State Route 190. While most of the water is diverted high in the canyon and used for electrical power generation before it is conveyed to the treatment plant by a penstock, the overflow water flows down to the mouth of the canyon and enters from the stream into the plant.
The first step of the treatment process takes place at the intake where heavy grit and sand is removed from the water. The water then goes to the traveling screens where the floatable material is screened out. Having removed the heavy, visible contaminants, now chemical addition takes place that disinfect and clean the water, The water then moves into the coagulation basin where the added chemicals are allowed to coagulate into small, chemical snowflakes that trap the dirt and other harmful materials. The sedimentation basin is the next step where the chemical snowflakes are allowed to settle to the bottom, leaving clean water on top. The clear water goes into the aeration weir where oxygen is infused to help remove any gases that could cause taste or odor problems, while the sediments off the bottom are separated and disposed. The final step is filtration through a multimedia filter to trap and remove particulates and microorganisms that did not settle out. This is a critical step since some protozoan that cause human diseases are very resistant to destruction with chlorine and in this process they are physically removed.
BCWTP has eight filters. Each filter has a filtering surface of 900 square feet with a maximum filtering rate of 5 gallons per minute per sq. ft., which gives each filter a maximum flow of 6 mgd. Normally the filters are operated at 4.5 gpm. Beneath each filter is a perforated floor that allows the water to pass through to an under drain system that takes the filtered water to the effluent line and then to distribution system.
On top of the under drain is a carefully engineered filter bed. The bed consists of a foot of gravel, a foot of engineered sand, and a foot of anthracite coal. The materials and their distribution are engineered to very strict specifications. This makes for a very efficient filter media bed that can take out the smallest particles, to below 1 micron in size, that have gotten through the sedimentation process. During operation, the filters are back washed periodically to wash out the trapped particles, transfer them to waste, and return the filter to optimal service.
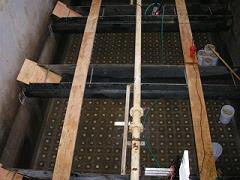
|
View of filter bottoms beflore the new media is installed. |
|
The BCWTP filters are 20 years old and have seen their life expectancy. A decision was made to replace them during the winter of 2007 when the water demand is at its lowest. . Before the media is replaced, all the old media has to be removed. To accomplish this task, a large vacuum truck was used to take out all of the old material and expose the under drain. The under drain is cleaned and very carefully inspected for any problems. The entire bed is then power washed in preparation for installation of the new media.
The first layer to be installed is the gravel layer. The gravel is graduated into specific sizes—2 ˝”, 1 ˝ ”, 1”, ľ ”, ˝” and 3/8 ”. The media is very carefully layered by size, in 2 inch lifts. The gravel layer is the most difficult to install because of the graduated size requirements in the layers, and care needed so as not to disturb the under drain configuration. Much of this work is hand work, time consuming and tedious.
On top of the gravel, one foot of sand is added, effective sizes being from 0.35mms to 0.65mms with a uniformity coefficient of 1.7 or lower, meaning that all of the sand granules are similar in size and shape. Finally one foot of anthracite, the effective size 0.6mms to 1.6 mms with a uniformity coefficient of 1.7 or lower, tops the filter.
With the filter media installation completed, the filter needs to be washed and skimmed of any residual material fines. The next step is to backwash the filter until it is clean. The media is then checked to be sure that the level is correct. Now the filter is ready to be disinfected. Water with a 50 ppm residual of chlorine is added and allowed to sit for 24 hours, then the bed is emptied, refilled and sampled for bacteria. If all goes well, the filter is ready to go back into service.
Filter media replacement is a time consuming and difficult process. One of the difficulties experianced during this job has been the cold weather. Not only does that make working in the filter unpleasant, but the bagged media kept freezing, making it hard to distribute into the filters. The project is going very well, in spite of the difficulties, and we anticipate having eight new filters on line in time for spring runoff. These new filters should provide another 20 years of exemplary performance
In 2006, all three Salt Lake City’s water treatment plants earned the EPA Partnership for Safe Water Director’s Award for five consecutive years of program compliance. |